Understanding Defoamers: The Essential Guide to Foam Control in Industrial Applications
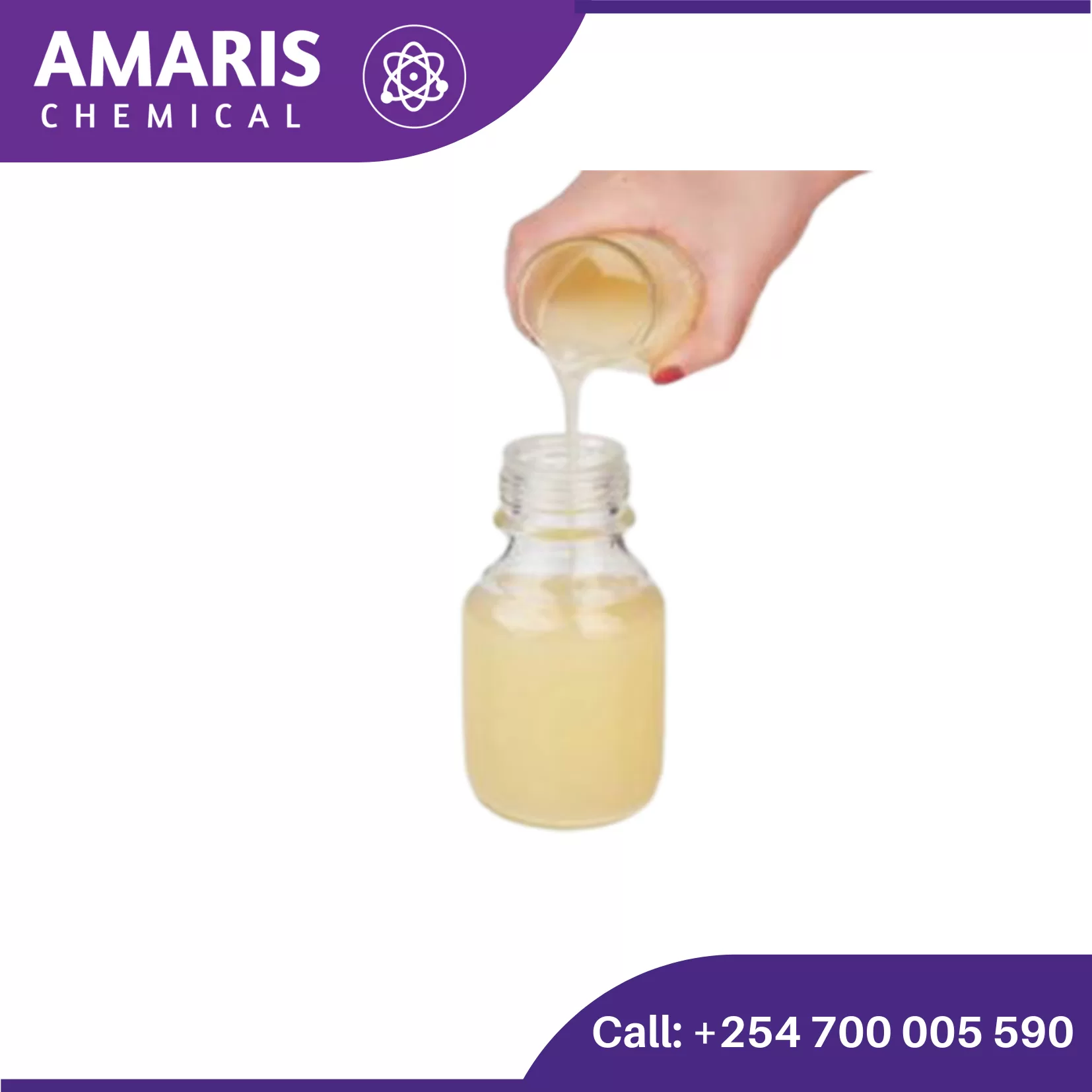
Foam can be a major issue in industrial processes, affecting efficiency, quality, and equipment functionality. Whether in food processing, wastewater treatment, or chemical manufacturing, excessive foam can cause serious operational disruptions. This is where defoamers play a crucial role.
What Are Defoamers?
Defoamers, also known as anti-foaming agents, are chemical additives that reduce or prevent foam formation in industrial processes. They work by destabilizing foam bubbles, causing them to collapse and preventing their regeneration. Defoamers are essential in industries where foam can interfere with production, such as pulp and paper, coatings, textiles, and pharmaceuticals.
How Do Defoamers Work?
Defoamers operate through three primary mechanisms:
- Breaking Foam Bubbles: They weaken the surface tension of foam bubbles, making them burst.
- Preventing Bubble Formation: They reduce the likelihood of foam forming by modifying liquid properties.
- Spreading and Coalescence: They spread over the foam surface, causing bubbles to merge and collapse.
Types of Defoamers
Defoamers come in various formulations to suit specific industrial needs. The main types include:
- Oil-Based Defoamers: These contain oils like mineral or vegetable oil and are effective in non-aqueous systems.
- Silicone-Based Defoamers: Highly effective in many industries, these defoamers work well at low concentrations.
- Powdered Defoamers: Used in powder-based processes, such as cement manufacturing and detergents.
- Water-Based Defoamers: These are eco-friendly and often used in food processing and wastewater treatment.
Applications of Defoamers
Defoamers are widely used across industries, including:
- Wastewater Treatment: Prevents foam overflow and improves efficiency in aeration tanks.
- Food & Beverage: Ensures smooth processing in fermentation and dairy production.
- Paints & Coatings: Reduces surface defects caused by foam in coatings and adhesives.
- Chemical Processing: Enhances mixing and prevents disruptions in manufacturing.
Choosing the Right Defoamer
Selecting the right defoamer depends on factors such as process conditions, compatibility with the system, and environmental impact. Silicone-based defoamers, for instance, offer excellent performance in high-temperature applications, while water-based options are preferred for food-safe processes.
Conclusion
Defoamers are indispensable in industrial applications where foam can hinder productivity and quality. Understanding their types and functions helps industries optimize performance and maintain smooth operations. By choosing the right defoamer, businesses can improve efficiency and reduce downtime effectively.